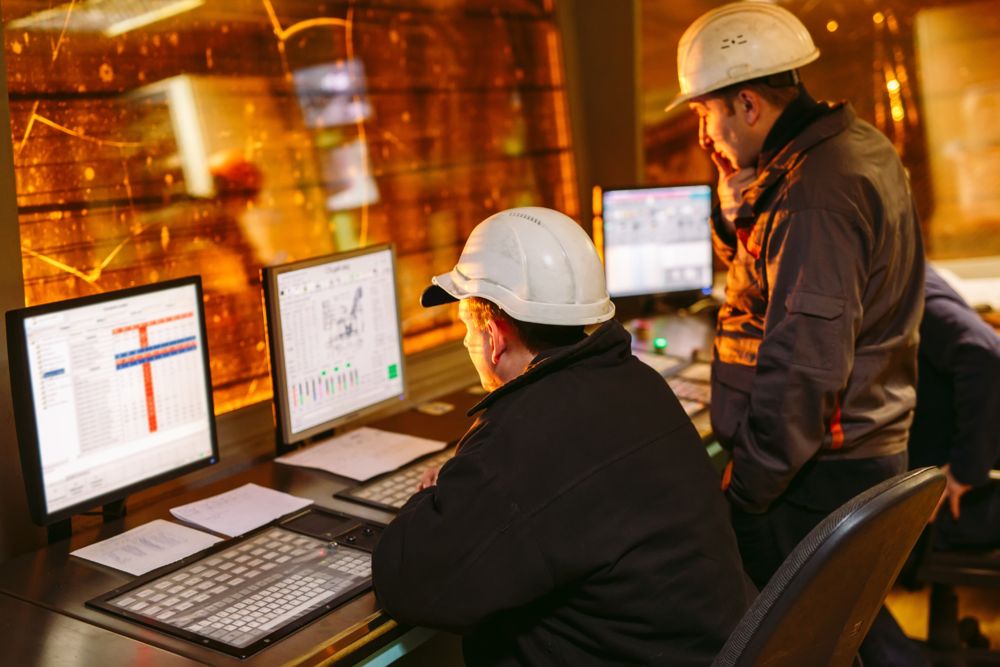
More efficiency and environmental protection thanks to the use of PLCnext Technology
The number of countries committing to achieving net-zero emissions in the coming decades continues to grow – the world still has a chance to limit the global temperature rise to 1.5°C. Such changes can be enabled by applying the open ecosystem PLCnext Technology in combination with the MLnext software to efficiently reduce emissions. Read in this article how technology can help achieve emission reduction in thermal process technology to enhance efficiency and environmental protection.
The EU aims to be climate-neutral by 2050, achieving an economy with net-zero greenhouse gas emissions. This goal, a core part of the European Green Deal, aligns with the EU’s commitment to global climate action under the 2015 Paris Agreement. The transition to a climate-neutral society is both an urgent challenge and an opportunity to create a better future for all. All parts of society and economic sectors will play a role – from energy, industry, and mobility to buildings, agriculture, and forestry.
Holistic Approach
To successfully implement long-term and sustainable climate strategies, all areas of industrial factories must be considered – from raw material storage and batch houses to individual production, packaging, and storage areas, and the building itself. Without this, efforts to reduce greenhouse gases or comply with environmental and materiality analyses will fail.
Energy-intensive industries such as steel, glass, ceramics, or non-ferrous metallurgy face the challenge of converting their existing thermal processes along the entire production chain to low or zero CO2 operations. This requires minimally invasive, open technologies that generate sustainable infrastructures while ensuring functional safety. At the same time, certified, open digitalization and automation platforms must be available for security. For the energy transition to succeed, thermal systems must be designed to operate with electricity from renewable energies or other future low-CO2 energy sources. Simultaneously, energy and plant availability, product quality, and economic efficiency must be ensured. Additionally, conventional heating concepts need to be rethought or reconsidered for low or zero CO2 process heat generation.
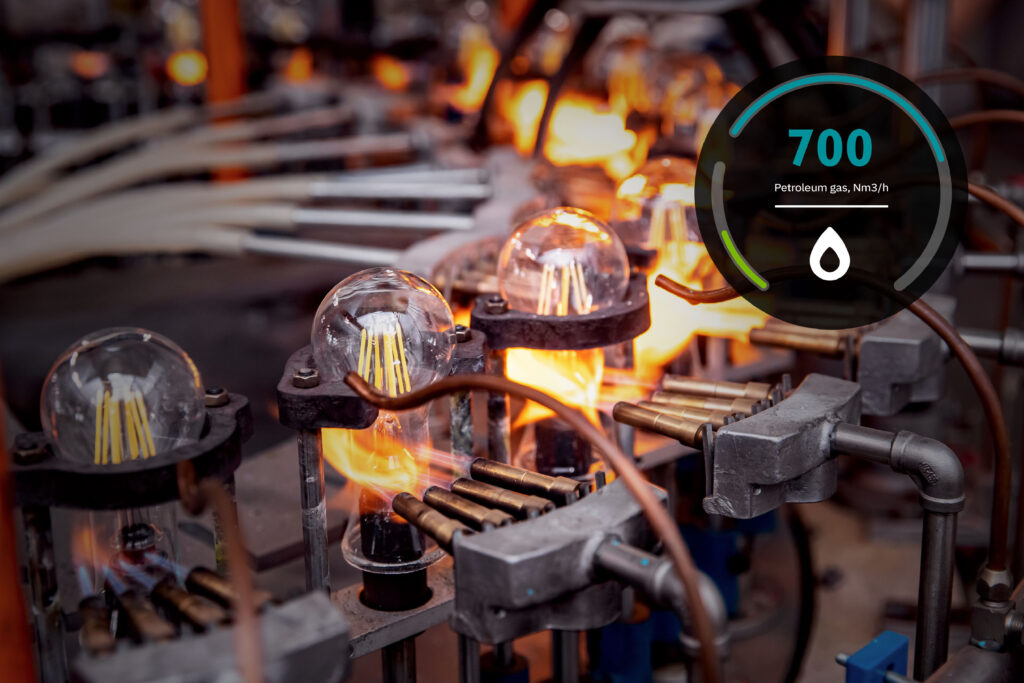
New Requirements for Industrial Firing with Hydrogen Gas
The Power-to-Gas (PtG) principle plays a significant role in modern gas and hydrogen networks as a new gas infrastructure source. PtG refers to the conversion of electrical to chemical energy (gas) through water electrolysis. The resulting hydrogen gas can be used both energetically and materially – for example, in industry and its thermal processes. This leads to new requirements for industrial firing.
Hydrogen and its mixtures also reduce air demand, change calorific value, increase combustion speeds and flame temperatures, and increase nitrogen oxides (NO) or nitrogen dioxide (NO2). This affects the “machine,” i.e., depending on the thermal process, the melting tank, furnace, or boiler, the supply technology (pipe network, stations, valves, sensors, mechanical actuators, storage, and control elements), the burner, and especially the control and automation system of the thermal process, if available.
Open Ecosystems Including Safety and Security
Thermal processes must be integrated into existing systems minimally invasively and with high yield. In the past, digitalization actors mostly thought of DCS, ERP, and MES systems, sensors, and factory machinery and equipment. Conventional, sometimes still mechanical equipment responsible for fuel-air ratio, flashback, ignition temperature limit, valve tightness, upper furnace temperatures, flame monitoring, minimal fuel consumption, and maximum flows and pressures were either overlooked or forgotten in bulky decentralized systems.
In the future, thermal process technology must meet the following requirements:
Agility can be increased through low or no-code applications for simple, individual, and scalable adaptation to changing fuel lines, using uniform parameterization platforms like the open-source tool Grafana.
- Mixed firing, control procedures, exhaust gas recirculation, fuel line purging, and more must be operated on open, holistic ecosystems/platforms
- Retrofitting and effective integration of sensors for fuel and exhaust gas analysis and new sensor generations are scalable regardless of the communication protocol
- The functional safety of the furnace, melting tank, or boiler goes hand in hand with cyber security according to IEC 62443 or NIS 2.0 requirements
- The operator can introduce machine learning (ML) and industrial IoT (IIoT) for condition-based monitoring and process optimization in their plant – both off and especially on-premise
- Agility can be increased through low or no-code applications for simple, individual, and scalable adaptation to changing fuel lines, using uniform parameterization platforms like the open-source tool Grafana
Preventive Maintenance with Machine Learning
By early detection of unusual behavior patterns, disturbances and changes in combustion processes can be avoided. This includes gas fluctuations, load curve adjustments, and effective control of actuators and dampers. For this purpose PLCnext Technology including the MLnext software solution, is used. The predictive approach also offers further potential economic and sustainable benefits:
- Higher overall equipment effectiveness (OEE) in thermal process machines – such as an IS machine in the glass industry – and thus a significant reduction in scrap
- Effective and smart operation of fuel-air ratios and electric heating systems by saving expensive external hardware, such as automata, tightness control systems, or temperature controllers
- Factory-wide intelligent and condition-based monitoring of the process, including safety-relevant sensors for measuring emissions, furnace, chimney draft, and hearth pressure, classic machine safety, and various temperatures and pressures
The PLCnext Store provides the MLnext machine learning system among many other apps. It helps professionals manage misbehavior in industrial firing and improve emissions predictively. For process optimization, MLnext only requires a controller or edge device with container visualization, such as a Docker-enabled PLCnext controller.
Comprehensive Certification
In this context, the OT security certification of the PLCnext Control product family by TÜV Süd according to IEC 62443-4-2, combined with existing safety certification, sets new standards. IEC 62443 is the internationally leading standard for OT security. The functional safety of the controllers complies with safety standards IEC 61508, ISO 13849, and IEC 62061. To realize successful automation solutions, both perspectives must be linked in the future. Due to the demand for tamper protection and the inclusion of remote access to machines and systems, the aspect of OT security is gaining more focus in the upcoming machinery regulation. The certified PLCnext Control product family already meets these requirements.
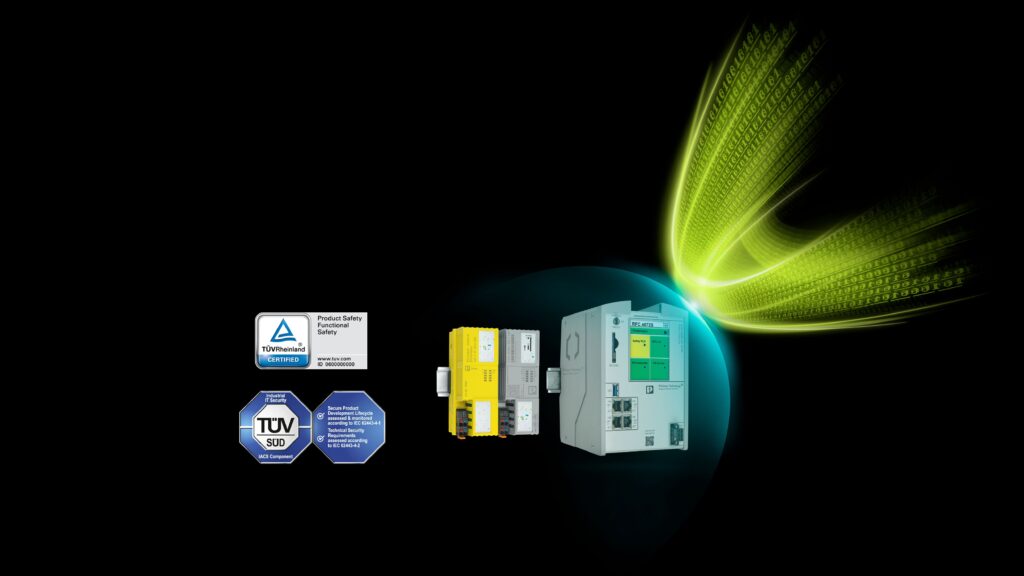
Additionally, turnkey and freely configurable thermal process control cabinets are provided. Signals can be processed directly in a safety-oriented manner, normalized, standardized, and sent bidirectionally in real-time via the free framework without additional data silos to the corresponding devices on the IT/cloud, ERP/MES, or DCS side. This saves the user space, hardware, and especially engineering time. If needed, the MLnext app can virtualize information from various media, sensors, actuators, fuels, and systems on-premise or in a downstream server of a cloud – for example, Proficloud.io.
This article was written by Markus Kick, International Business Development Manager, Digitalization and Thermal Process Technology, Phoenix Contact Electronics, Bad Pyrmont
On this website, you will find more information about our open ecosystem PLCnext Technology. In exciting use cases, we discuss already realized applications and address specific challenges. Additionally, you will find all the information about the individual ecosystem participants PLCnext Control, Store, Engineer, and Community, as well as many news and articles about this technology.
Feel free to contact us if you have any questions.