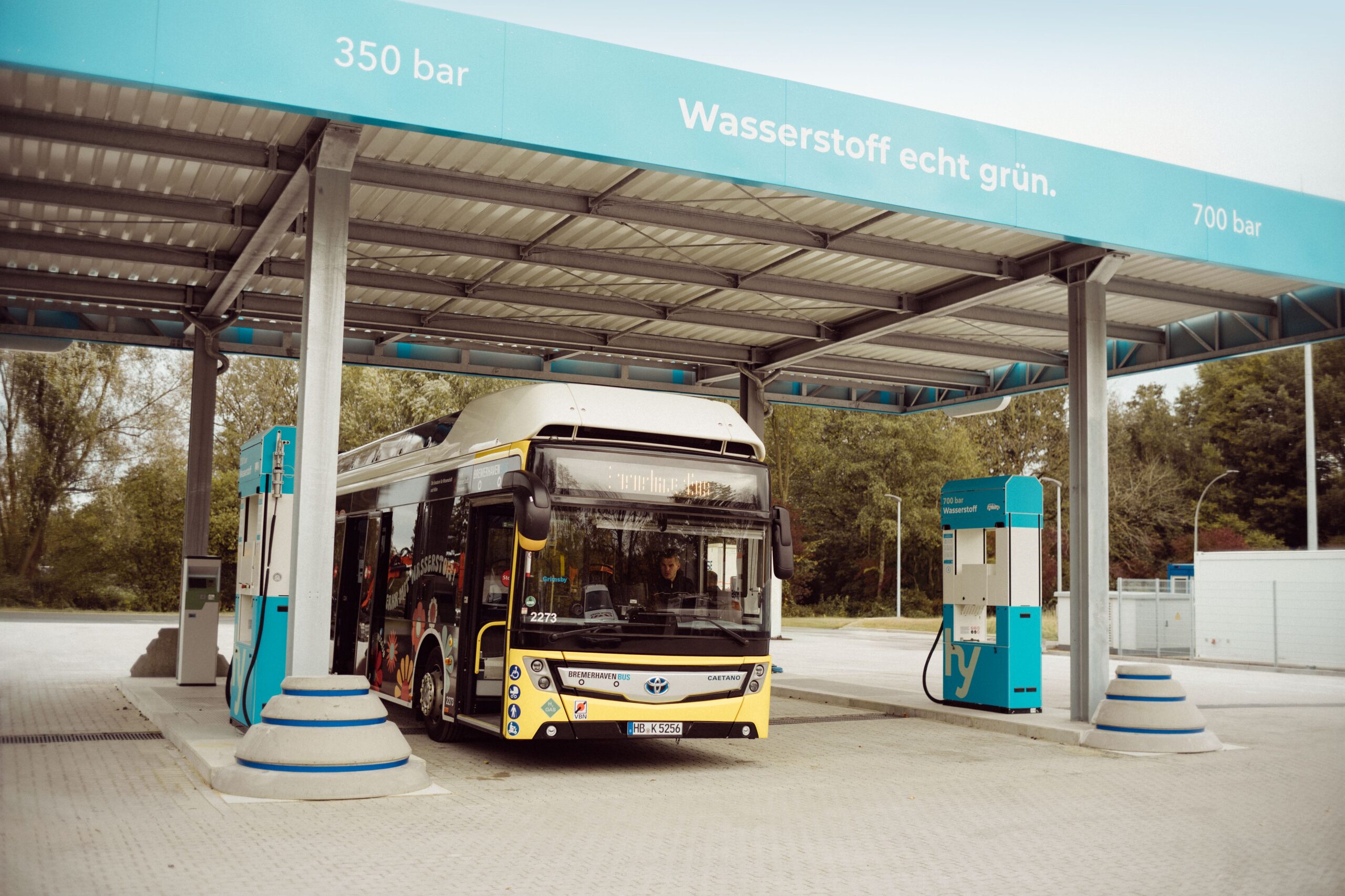
Automating green hydrogen is currently at the center of public and professional discourse—featured on TV and radio, in newspapers, online platforms, and at industry events. As hydrogen gains momentum as a clean energy carrier, the role of intelligent automation becomes increasingly vital.
It has always played a significant role. It is not only the most abundant element in the universe—accounting for about 75% of visible matter—but also a key component of our planetary system and the sun. In its purest form, hydrogen is very rare on Earth, but it is most commonly found in combination with water or other organic molecules.
Because its combustion produces only water, hydrogen is considered the energy source of the future and the cleanest energy carrier available. It plays an increasingly important role in climate-neutral mobility and is therefore a highly relevant topic in the energy sector.
Hydrogen is also gaining momentum in Bremerhaven, Germany, where this energy carrier is quite literally providing a tailwind on the path to climate-neutral transportation. At the Grauwallring industrial estate, HY.City.Bremerhaven GmbH & Co. KG uses a wind turbine to power the on-site electrolysis of hydrogen.
From Wind to Wheels: A Complete Green Hydrogen Chain
The so called ´green hydrogen project´ was realized by GP Joule, the system provider for integrated energy solutions which acts as the general contractor. The production of green hydrogen is part of a regional hydrogen ecosystem and is considered a lighthouse when switching from fossil fuels to renewable fuels. Automation technology from Phoenix Contact is used to ensure sector coupling with high availability and a secure remote connection. It makes economic sense for Germany to continue pursuing hydrogen technology, so that it can maintain its standing as a global center of business.
So far – at least according to the opinions expressed by industry experts in the German ZDF business news program ´Wiso´, which was broadcast in the summer of 2024 – the chances are good that the German SME sector will be able to play to its strengths and become a global driver of the energy transition with hydrogen.
But how is this possible? By industry and investors showing that it works – as it does in Bremerhaven, for example. Here, GP Joule has implemented a complete value chain for green hydrogen for HY.City.Bremerhaven – from electrolysis as a key technology, through compression and storage in mobile tankers, right through to delivery to the service station and the right fuel cell buses for public transport. Only the wind turbine generator, which supplies energy to the electrolyzer, was already in place on the Grauwallring industrial estate, having been installed several years ago.
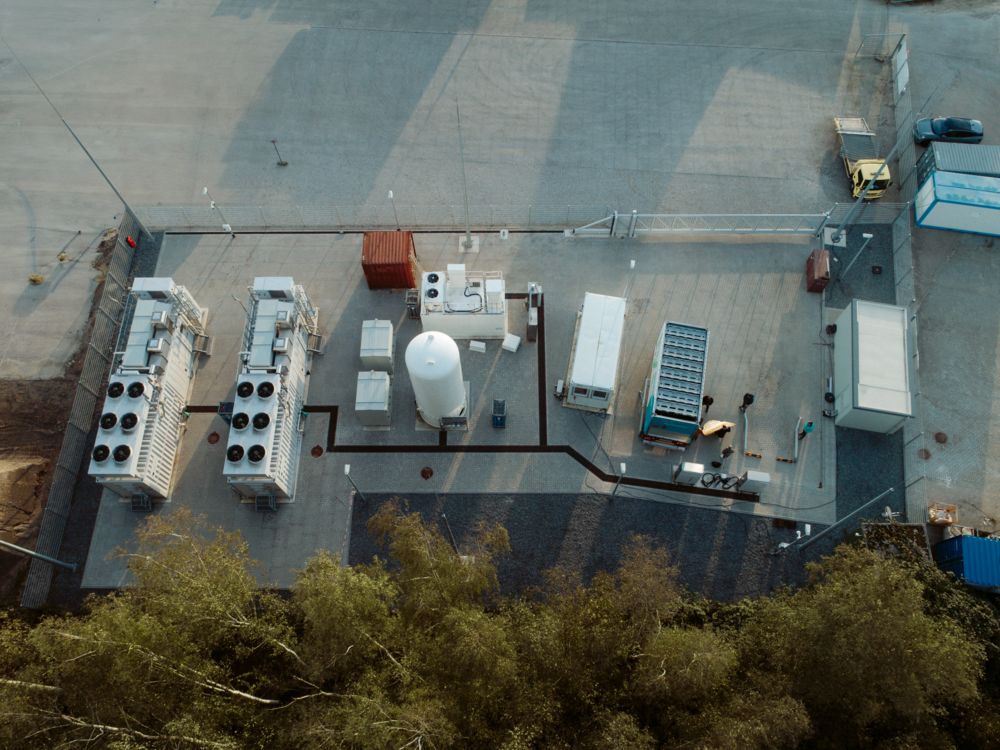
Technical support for the entire value chain
What are the main challenges currently faced in the supply of hydrogen? According to GP Joule, solutions must provide the right type of energy in the required quantity, at the best location, and at the exact time it is needed. For hydrogen as an energy carrier, this means that, from a holistic point of view, it is not enough to focus your expertise on individual process steps; rather, the entire value chain and logistics must be included. This is precisely where the strength of the system provider from Schleswig-Holstein lies, putting its own expertise in hydrogen mobility into practice on the road. GP Joule did just that in Bremerhaven, by creating the HyRunner – a mobile storage system for intelligent hydrogen transport from the electrolysis site to the service station or to industrial customers.

“The two electrolysis containers at the base of the wind turbine generator operate at full load, each with an electrical output of one megawatt. From this, electrolysis produces up to 900 kilograms of hydrogen per day, which fills one of the tankers in around six hours,” explains Marian Hieke, Head of Engineering at GP Joule. The tank and storage system operates at 380 bar pressure. Compressors are used to compress the hydrogen obtained from electrolysis, which is at an initial pressure of 30 bar. It is first transferred to a buffer storage unit and from there converted to the desired tank pressure.
Cost-Effective Automation Kit for Ex and non-Ex areas
As mobile storage and transport tanks, hydrogen trailers play a central role in the process chain. The vehicles contain a large amount of control and interface intelligence, which is housed in a robust stainless steel control cabinet. The production and use of hydrogen raises various questions about explosion protection (Ex). To avoid the risk assessment leading to a situation where the entire automation system consists of expensive Ex components, a functional modular system is recommended. This covers both Ex and non-Ex areas economically. In the Bremerhaven project, Phoenix Contact only equips those processes that actually require Ex protection with Ex I/O modules from the Axioline product family. For example, input cards are used in the HyRunner for the valves of the hydrogen lines. They can be used to wire the signals directly to the correspondingly certified I/O modules. So there is no need for separate Ex impeding devices, which saves valuable space and reduces costs. Outside of the Ex zone, the standard I/O portfolio from the Axioline modular system is sufficient – and there are no functional limitations due to the consistent overall system.
Secure Data Transmission to the Cloud
A large amount of data is generated during the various processes, which can be stored in a cloud and used in a variety of ways. Data is transmitted to the cloud via an industrial cellular router from the TC Router 3002T-4G series installed in the control cabinet. The TC Mguard RS4000 router provides the necessary IT/OT security. With this equipment, the roadworthy storage system is able to communicate independently and securely with the cloud, enabling time-efficient refueling in coordination with the upstream electrolysis and storage processes. “For example, we can determine fill volumes, control valves, and track the current location of the trailer via GPS,” explains Marian Hieke. “The functions are supplemented by a system integrated into the PLCnext Control for the calibration-law compliant billing of the supplied hydrogen.”
Although the HyRunner is designed to supply Bremerhaven’s hydrogen-based public transport system autonomously, it fits seamlessly into the entire process chain from a digitalization perspective. PLCnext Control is also used as the highest control instance at the location of the electrolyzers. The so-called location controller collects all operating data of the process chain, from electrolysis through to the tank trailers, and forwards it wirelessly to a central evaluation unit via the TC Mguard router and an antenna.
High Availability through Redundancy
When it comes to the technical equipment of data logistics – referred to as HySite – availability is extremely important. Failsafe performance is technically ensured by two Quint4-PS power supplies in conjunction with a redundancy module from the Quint-Oring product family. The solution is supported by five battery modules, which together with a Quint4-UPS form an uninterruptible power supply. In this way, short-term power failures can be bridged or the entire system can be shut down in a controlled manner in the event of a malfunction, without it reaching a critical state due to the high reactivity of hydrogen. The two control units also create a high-availability redundancy pair via the applicative system redundancy (ASR) concept from Phoenix Contact. The availability solution is rounded out by the network, which connects the individual submodules of the location to each other and, due to its ring structure, is failsafe against individual faults.
Further use of (waste) Heat and Oxygen
The production of renewable hydrogen from wind power represents the beginning of hydrogen-led mobility in Bremerhaven. Since considerable amounts of (waste) heat and oxygen are generated during electrolysis, the visionary entrepreneurial consortium behind HY.City.Bremerhaven is already thinking about how to use both economically. According to the project team, a local district heating network is suitable for utilizing the 340 kW of (waste) heat, especially as there are sufficient commercial and industrial consumers in the immediate vicinity. The further processing of the oxygen is also on the agenda.
The potential of hydrogen is vast and offers many opportunities, especially when it comes to climate neutrality and net-zero goals.
More Information
We´ve created a video for this use case described here, which you can finde on our YouTube Channel.
Are you interested in reading more about emission reduction overall? Feel free to read one of our new blog posts ´Emission Reduction in Thermal Process Technology´.