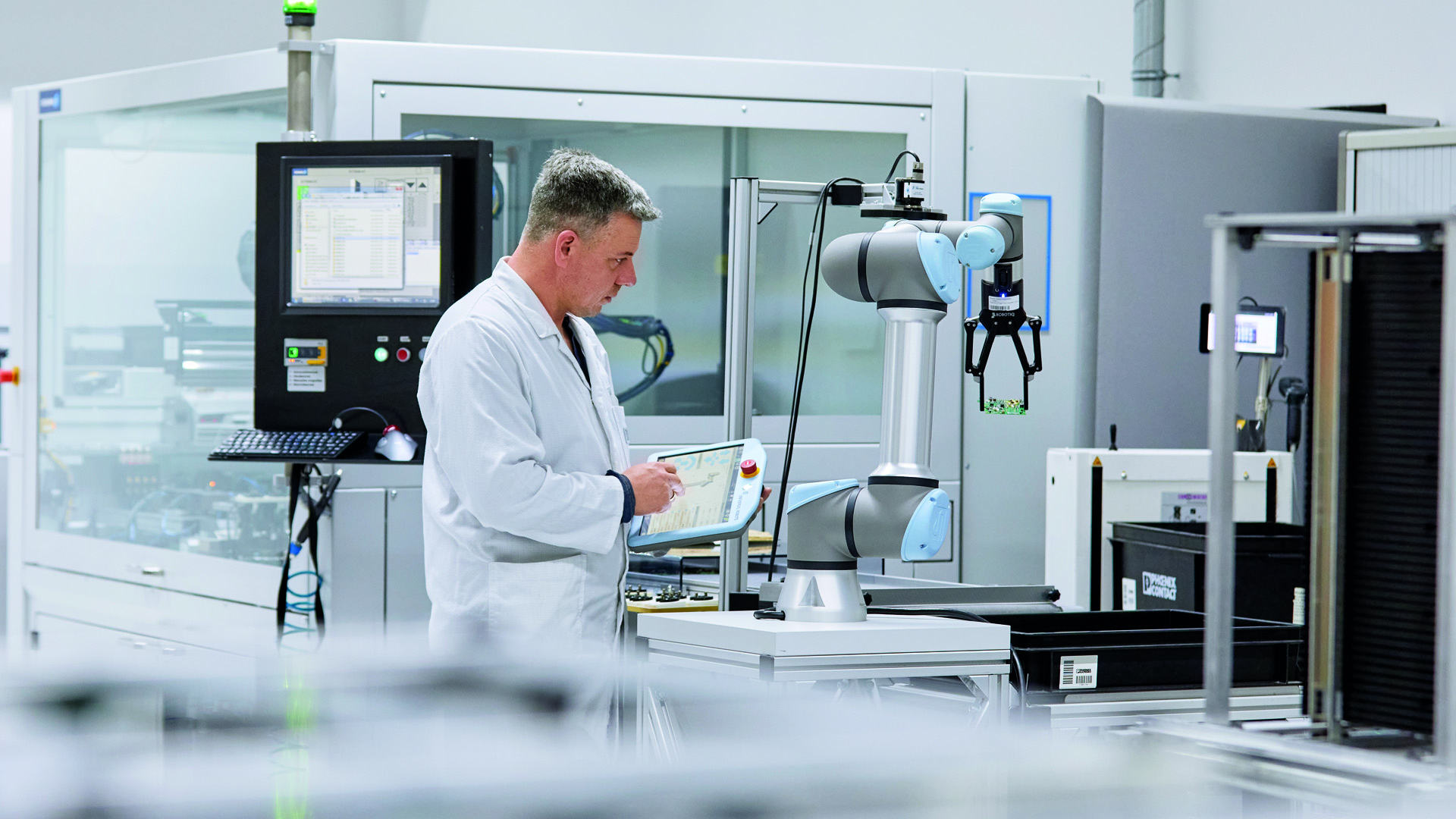
Alexander Kost works as a robotics engineer in the manufacturing engineering interface department of Phoenix Contact Electronics GmbH in Bad Pyrmont. The future has already been at this place for a long time: Alexander Kost has successfully accompanied the introduction of two cobots into the production processes of electronics and plastics manufacturing, thus setting an important milestone on the way to digital production. He says: “From my view, the cobots are an enrichment for every production employee as well as for the company itself. They are a support for the employees and guarantee a future-oriented competitiveness. Cobots have the potential to make Germany more attractive again as a production location and bring back production from abroad. A cobot can also become an irreplaceable support when it comes to digitization because a cobot is usually equipped with the latest control and safety technology, which increases flexibility and mobility in productions and greatly simplifies programming in contrast to a conventional industrial robot”.
Cobots (short for collaborative robots) are no longer science fiction, they are reality in many manufacturing companies. The stumbling blocks on the way to this reality with cobots are not necessarily those you think of at first. Detailed planning, financial investments and building up know-how can be critical points. But: The involvement of the employees is at least as important. Because: When the cobot is purchased, it has “learned” the first steps and is now ready for its use in production: If the employees cannot collaborate with the cobot, cost accounting and expert knowledge are of limited use.
So, there are many points to consider when introducing cobots. Discover what these points are and how you can avoid stumbling blocks in the following blog post so that the cobot goes well in your production.
The planning
In the first place, there is certainly everywhere the desire and the necessity to change something. For example, when production processes that are a burden on employees (e.g., due to recurring work steps in an unergonomic posture) cannot be fully automated. If this leads to a need for action and the use of a cobot is considered, this is the first step. However, it does not mean that the cobot will be used at exactly this production step.
Attention, first stumbling block: Finding the right place for the cobot
In order to be able to judge objectively and fact-based, at which production step the cobot makes the most sense, a comparison of pairs and a utility value analysis can be helpful. These tools are not only used for decision making, but can also support later steps. Namely, when it comes to creating an overview of the applications (especially those preferred by the employees) and acceptance within the company.
Once you have identified the most suitable production step, the search for the appropriate manufacturer and, if necessary, integrator begins. An integrator is an external service provider who takes over the integration of plants (and thus also of cobots). The integrator is usually not bound to one manufacturer and is more independent with a large portfolio of possible solutions. You should consult internal (if available) and external experts. With the supporting experience and knowledge of the experts, you can, for example, carry out an FMEA (Failure Mode and Effects Analysis), which provides you with the basis for a smooth implementation and use of a cobot.
Attention, second stumbling block: Inform works council and safety officer in good time
Before the actual investment, it is absolutely necessary that you communicate with any existing work council and safety representative. Because: If the working conditions and the working environment for the employees change, the work council has the right of co-determination.
You should also create a security concept before implementation. The safety concept describes how the risks to the environment (man and machine) from (un)foreseeable hazards are minimized, e.g. by using ground laser scanners or light grids. The safety concept is later used for the risk analysis and finally for the risk assessment.
The Implementation
Before implementation, all members of the project team, the specialist departments, production managers, employees, safety officers and, if applicable, work councils must be fullfilled and the general conditions (operating resources concept, cost planning, responsibilities and time frame for the respective work packages) must be clarified. And as soon as possible!
Attention, third stumbling block: Involve the employees
The employees from the respective production lines should not only be informed, but also interviewed. Their experiences could provide new insights and can reveal certain challenges in advance.
Without official paperwork it is not possible: all relevant documents including signatures must be obtained. Relevant documents are e.g.:
- Production process changes
- Specifications and requirement specifications
- FMEA
- Release protocols
- Checklists for equipment safety.
When all documents and approvals are available, the actual implementation takes place: The cobot can move in. The implementation includes the following steps:
- Release of the equipment concept
- Design release
- Initial sample test report
- Preliminary acceptance by the integrator
- Transfer of equipment incl. final acceptance
- Serial release
Attention, fourth stumbling block: CE declaration of conformity and operating instructions
The system may not be operated without a valid CE declaration of conformity and operating instructions. The preparation of these documents takes time. Therefore, do not start too late!
The project manager coordinates the handover, final acceptance and release between the production managers, the integrator, facility management, environmental/safety experts, purchasing if necessary, as well as IT and the works council.
During implementation, all involved employees must be given comprehensive training.
The operation
First, the safety concept must be in place before the cobot is selected and implemented. Of course, standards and guidelines play a decisive role here. Since the technologies of the cobots are still relatively new, the standards and guidelines are constantly changing. What is marked as forbidden today may be possible next year (and vice versa). Therefore, even when the cobot is functioning well, you should stay in touch with internal and external experts and train all involved parties regularly.
Attention, fifth stumbling block: Regular training
As with most plants, implementation is always followed by challenges and optimization – even with cobots. Also for this reason, it is important to train all involved parties regularly. So that they can confidently meet the challenges and improvement potentials.
Do not be discouraged by mistakes, supposed weaknesses and potential for improvement and stay on the ball. After all, the results and experience gained will not only have a positive effect on production, but also on all departments involved.
If you successfully master these five stumbling blocks, the cobot will be well received and become a visitor who is welcome to stay. Welcome to the future!